Battling the Unknown
Boh Sidesteps High River, Unseen Obstructions to Boost Barge Capacity at Mt. Airy Plant with Dock Construction Project
Boh Bros. Construction Co. found itself battling high river levels and unseen obstructions during a floating barge dock construction project and associated pipe rack in Mt. Airy, LA last year.
In the end, the terminal Owner and the Operator significantly boosted their dock capacity to accommodate four 54- by 300-foot barges at one time. The terminal, situated just south of the Gramercy Bridge, ships oil, liquid asphalt and light oil to destinations along the Gulf of Mexico and Eastern Seaboard.
John Hambrick, manager of construction and engineering for the Owner, says the facility was at a critical juncture, as insufficient barge capacity at the site was causing the plant to miss out on potential revenue. “We were paying barges to sit and wait because we didn’t have the capacity that we needed,” he says.
Hambrick, who manages large construction projects for eight terminals from Texas to Virginia to Chicago, was immensely pleased with the outcome, as the multifaceted Boh Team was able to quickly respond to a host of unexpected challenges. “They did an excellent job —despite a few rough patches that no one could have anticipated.”
As many as five Boh crews worked side-by-side in tight quarters to tackle work that included civil, structural, marine, and foundation phases. By the dock construction project’s conclusion, the contractor had fabricated and installed a new floating barge dock with a 100-foot-long articulating truss; two 54-inch-diameter captive barge monopiles; eight 54-inch diameter barge breasting monopiles with laminated wraps; a truss tower; and 800 feet of structural steel pipe racks and supports for a highway and levee crossing.
A Skillful Approach to Dock Construction
It wasn’t an easy task, as Boh had to circumvent a variety of hurdles. Topping the list —the Mississippi River was at flood stage for an extended period of time at the project’s outset, significantly narrowing the project team’s work window. ”We had originally planned to begin in February 2019,” says Kyle Alexander, Boh project manager. “That was delayed until September due to the abnormally long high-river season we had last year.”
That left mere months for much of the work to be completed. Once the river dropped below Elevation +11 feet, multiple crews began working simultaneously to make up lost ground by constructing levee foundations, hydroexcavating pile locations within the plant, site clearing the river batture, pile driving, and erecting structural steel for the pipe rack and walkway.
Water proved to be an ongoing problem. Whenever it rained, operating construction equipment on the levee and batture was nearly impossible, so a temporary road was constructed using existing material on site —riprap, sand etc. —to enable cranes and other equipment to safely grab piles, erect steel, or place material.
Through it all, time was of the essence. “We knew that once the river came back up, we weren’t going to get back out there until the next season, which could last through October 2020,” Alexander says.
A Boh team led by Larry Lamonte and John Paul Talkington discovered numerous below-ground obstructions during the hydro excavation process, forcing the layout team to re-work and re-map the pipe rack foundation almost daily. Unfortunately, there were no subsurface schematics available for the decades-old site. “It was a recurring process where we would find obstructions, map them, and re-work the layout,” says Boh layout manager Mike Langlois. “We would shift the orientation of the piles, when possible, so that they would fit between all the obstructions.”
Only through a rigorous, collaborative process between Boh and the dock construction project’s engineer, Lanier & Associates, was the project team able to minimize impacts to schedule.
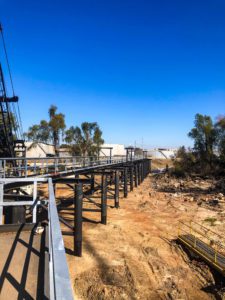
Darren Torres, Boh’s civil project manager, says working with the design team to integrate the new foundations on the existing levee was also a challenge. “Before we arrived on site, we worked closely with Lanier & Associates to eliminate potential conflicts. That advance work helped the entire dock construction project team be successful once on the ground,” Torres says. The civil team constructed seven poured-in-place spread footings, along with a concrete base, walls and a top concrete slab, as support for the pipe rack.
Due to these challenges, Boh’s Mike Langlois and Craig Sanchez took the initiative to plot control points and create new “as-builts” of the entire site. “All of the data was entered into our program, and we were able to more accurately generate new layouts of the work,” Langlois says. “Lanier then blended their design with our information so that they knew exactly where everything was located in conjunction with the new control points.”
Design precision was critically important given the tight spaces in which the team had to work. During pile driving, for example, a forklift and rough terrain crane were used to maneuver and drive 18-inch-diameter, 60-foot-long piles for the pipe rack around tanks, power lines, and other obstructions. The steel pipe piles were driven in two pieces so they could be easily maneuvered through the existing plant site.
By Land and by Water
Boh’s Kari Hubbard and Josh Menier, along with William St. John and Ricky Tamor, were responsible for designing and detailing the steel needed for the articulating truss, pipe racks, levee and road crossing, all of which was fabricated within Boh’s 12,000-square-foot, AISC-certified High Bay fabrication facility at the Almonaster yard.
“A lot of quality control checks were involved, particularly in regards to the steel connections,”
Alexander says. “We needed to ensure that everything was constructible upon arriving at the site. They did an awesome job from shop drawings to fabrication to shipping.”
The steel work culminated with the setting of a structural steel pipe bridge across Hwy 44 (River Road) during an around-the-clock, weekend-long closure. The steel for the 20-foot-wide bridge was shipped to the site and preassembled on the levee batture.
Steve Menard, steel foreman, says the bridge was lifted and placed in one section by a hydraulic crane. The bridge also supports a prefabricated steel catwalk for plant workers to access the dock from the plant, and vice versa. “Pre-assembling the bridge saved a significant amount of time and manpower,” Menard says. Others supervising the steel work were Max Bourgeouis Jr., Steve Ngyuen, and Matthew Vessier.
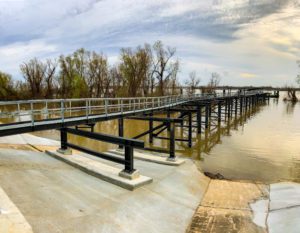
Meanwhile, Boh’s marine team, led by David Perry, drove mooring and berthing piles, and set a 100-foot-long articulating truss with a Manitowoc 4100 ringer crane in preparation for the project’s centerpiece—a floating barge dock. The process followed stringent quality control measures, as the team double and triple checked pile locations to ensure their accuracy and alignment.
Driving piles in a moving river is no piece of cake, and the work at Mt. Airy was no different. “The river was high and we were in a bend, so it was a challenge to make sure that the large mooring piles were in the right location,” says Couser Hano, field project manager. To ensure accuracy, a Boh survey crew frequently “shot locations and checked everything three times before we actually put a pile in the ground.”
The marine crew monitored for any pile movement throughout the process. “We had to stay on top of that,” Hano says, “because we had riprap underneath the mudline that we were driving through…you could literally hear the rocks crunching underneath the piles as they were going into the mud.”
Langlois says driving in the river is always difficult from a design layout standpoint. “You’re driving off of a floating structure, the river is moving, and once you put your piles down the barge wants to move on you a little. I was very conscious of that from the start.
“Also, the bottom of the river is not perfectly flat, so your pile wants to slide on you,” Langlois adds. “Fortunately, there are things you can do to adjust.” The Boh team worked with the engineer to adjust berthing pile locations when problems arose. “Fortunately, we only had to make a few small adjustments in this case.”
Pride in the Team
In his 40 years of working in construction, Hano has never been more impressed by the work ethic displayed at the Mt. Airy site. “We had multiple crews out there at the same time on a tight site, with a lot of underground obstructions…it could have become a nightmare,” Hano says. “We would get three quarters of the way done, then find an unknown obstruction and have to start back over, backfill that area and try something else.
“Despite all that, no one got frustrated…all we could do was just keep moving forward.” He was particularly impressed by first-time foreman Garrett Robertson and his ability to roll with the changes. “I know it sounds like a cliché, but it was a team effort,” Hano adds. “This was great to be part of a job that, even though it was broken into separate parts, we functioned as one team…and we did it safely.
“Literally, nothing slowed us down. Everything rolled as one.”
This article was originally published in The Boh Picture. To read about more of Boh Bro’s projects, click here.