A Seamless Handoff: Boh Bros. Helps Bunge Out of Tight Spot
For over 60 years, Bunge has handled an assortment of agricultural products from its export terminal along the Mississippi River in Destrehan. It’s one of five such ports in North America that the company uses to export soybeans, corn, wheat and sorghum to customers around the globe.
As the Destrehan facility’s conveyor system approached the end of its service life, Bunge began designing a replacement that would not only allow it to continue operating, but do so more efficiently and productively. The existing conveyor was experiencing sporadic shutdowns and mechanical repairs—impacting operations.
Consequently, Bunge initiated design of a new conveyor system and dock, advertised for bids and awarded a contract to build the new structure.
Bill Cloyd, Bunge project manager, says that’s when things started going downhill, as a lengthy delay in the U.S. Army Corps Engineers permitting process forced designers back to the drawing board. The Corps wanted assurance that the levee would be protected during construction and prohibited the construction of any crane supports along the river side of the levee, referred to as the batture.
To comply with the permit, Bunge began designing an innovative trestle system as a work platform for cranes, other equipment and permanent access to the new dock, and agreed to reinforce the levee by adding stone revetment within deepened areas of the river bottom at the project’s conclusion.
Cloyd says time became the real enemy. “It was over a year before they gave us that notification and by the time we redesigned and re-estimated the job, we were pushing two years.”
Once Boh Bros. was awarded the project in 2015, the design and fabrication of the trestle system was already complete, and there were only 20 months remaining until the deadline for commissioning and startup. Bunge’s Construction Manager, APTIM Senior Program Manager Andrew Knapp, says the New Orleans contractor was a lifesaver. “I loved Boh coming in,” he adds “They immediately said, ‘This is what you’ve designed and as long as we don’t see any major flaws, we can put it in.’”
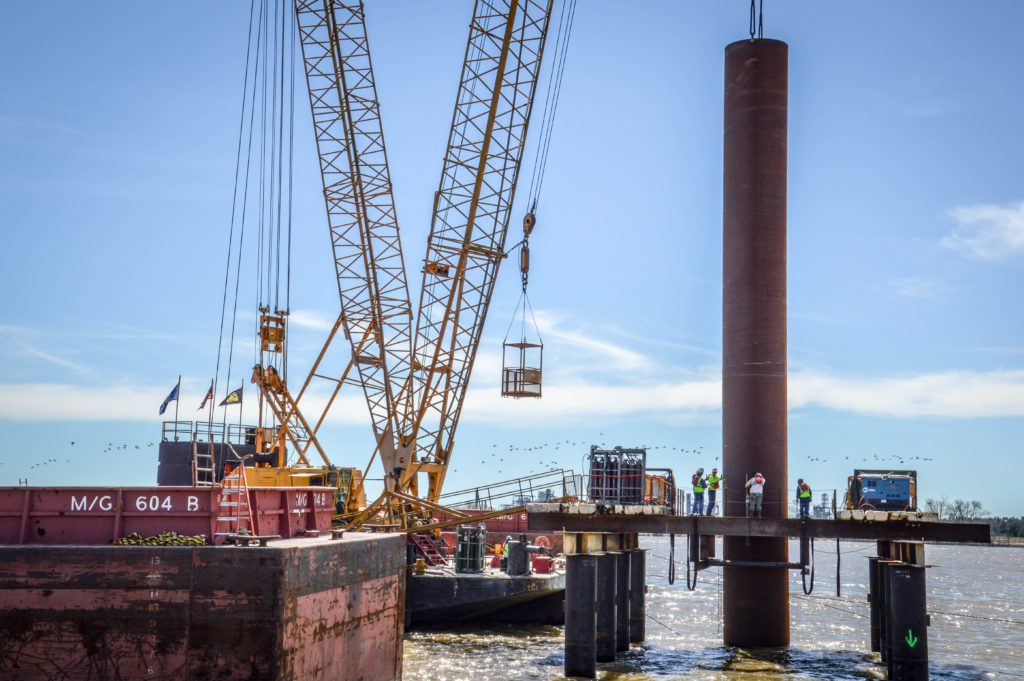
It was a unique situation for Boh Project Manager Patrick Ledet, because nearly all of the project materials had already been procured. This situation required a great deal of flexibility on Boh’s part, as it had to adapt its own work processes to conform to a project that had started then stopped due to the permitting delay. “All of the piles were in hopper barges on the river,” Ledet says, “and the structural steel was at the fabricator’s yard in Tuscaloosa.” Because the steel piles had been sitting on barges for nearly a year—at significant expense to Bunge—they were sent to Boh’s Almonaster facility for stockpiling.
Within days of the contract award, Boh mobilized its crews and moved into an existing trailer complex provided by Bunge immediately. “On day one, we began staging the ringer crane,” Ledet says. “We also began receiving materials that had been stockpiled by the suppliers.”
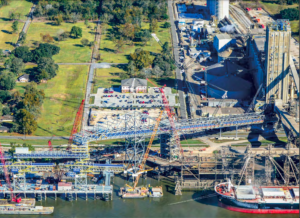
A Logistical Feat
APTIM’s Knapp, who has been on the Bunge job in some capacity since 2012, says there were other design challenges even without the stringent Corps requirements. The need to keep the existing grain conveyor operating during construction mandated that the new system be designed at a 45-degree angle across the levee—facilitating an eventual tie-in with existing land-based operations.
“The result is a massive cantilevered system with a huge truss that spans a road and levee,” Knapp says. “So we had to tell the Corps that we wanted to build a 40-foot-wide, 1,000-foot-long truss across their levee. That was difficult.”
Boh’s first point of attack was the conveyor system’s structural steel drive tower, which would become the nerve center of the entire project as it houses the compressor room, main electrical room, switch gear for incoming power and main conveyor drive motors. Boh drove 16 steel pipe piles as support, measuring 48 and 60 inches in diameter and 175 feet long, followed by a large, elevated concrete platform.
Continental Construction Co. of Memphis performed the structural steel erection and mechanical installations for the conveyor system, while Boh Bros. self-performed the work from the anchor bolts down. “The real story here is that we came in under a very tight schedule on a highly technical job, mechanically speaking, working with a major subcontractor (Continental) that we had never worked with before,” Ledet adds.
To complement the new conveyor system, Boh constructed a 468-foot-long by 53-foot-wide steel pipe pile-supported, reinforced concrete dock about 200 feet from shore. Arranged as a grid, transverse concrete beams connect the dock’s multiple concrete bents, and heavy duty grating provides the dock surface. Additionally, three 84-inch-diameter monopile mooring dolphins and six 96-inch-diameter monopile breasting dolphins, equipped with high capacity bollards and fender systems, offer support for the massive ships that dock there.
Throughout the process, Boh provided constructability input where appropriate. “The original design called for the installation of rebar rings inside each pile as a way to secure the pile plugs to the rest of the dock structure,” Ledet says. “However, with small diameter piles, it’s difficult to make that work. We showed them that the math still worked if we welded something on top to more or less serve the same purpose.”
Scheduling Challenges
As an added wrinkle, extenuating circumstances impaired an already aggressive schedule. On two occasions, high river levels and other weather-related issues delayed work for weeks at a time. Boh also had to work under active ship traffic, as Bunge’s existing ship loading system remained in operation. “We developed a good working relationship with Bunge’s Gulf Operations director (Cal Williams),” Ledet says. “The relationship hinged on developing trust, where we could tell him in three to four weeks we’re going to do ‘X’ and know with certainty that it was actually going to happen.”
Through it all, communications reached an unprecedented level, as Boh managed a crew that reached nearly 150 at peak times. The contractor used three-week look ahead meetings and pull-planning sessions (aka Sticky Note sessions) to “micro-schedule” Boh crews and subcontractors, which was necessary to cohesively attain interim milestones such as barge deliveries, barge crane moves, critical lifts and area trade changes. “In the end, if we missed the owner’s shutdown/startup dates, we would not be successful,” Ledet says.
Safety was another ever-present concern. “Working over fast-moving river currents comes with certain hazards,” Ledet says. “When you have a fully-operational, existing facility nearby loading ships, a guy falling in the water could be sucked under a vessel within seconds.” As a solution, Boh “stacked” barges side by side and used gangways between them to enable workers to walk to their work area from land, thereby minimizing the need for crew boats. As an added precaution, Boh installed fixed handrail systems around the perimeter of the barges.
Boh’s safety plan also extended to the general public, as it had to circumvent a bike path that traversed the top of the levee, while ensuring that cyclists and pedestrians remained safe even as heavy truck traffic accessed the site. “The bike path was running straight through the planned temporary Acrow Bridge location, so we had to get creative,” he adds. “We decided to jog the location of the bike path a bit and put in an asphalt detour with concrete barriers and handrails.” The plan was successful—there were zero incidents with the public throughout the project.
Startup of the new conveyor system early last year brought its own challenges as Bunge sought to minimize shutdowns. “It began with a four-week partial shutdown, followed by a four-week full shut down, a three-week partial startup and a three-week full startup,” Ledet says. “The full shutdown was 24 hours a day, seven days a week; all other periods were 12 hours a day, seven days a week.”
Now fully operational, the new conveyor system replaces the existing system, improving Bunge’s efficiencies. “It’s a much better technology for loading ships, and we—as well as our clients—stand to reap significant benefits as a result,” Cloyd says.
This article was pulled from The Boh Picture. You can read more about Boh Bro’s projects here.