Houston, We Have a Project
Boh continues to showcase its abilities with successful design-build project by assisting Vopak Moda with building a new dock facility in the Houston Ship Channel.
Vopak Moda Houston (VMH) desired a single point of contact and reduced risk, so the marine terminal operator chose the design-build method to construct its new dock facility in the Houston Ship Channel. Boh, with a long list of successful design-build and other alternative delivery projects, stepped up to the plate to help meet the owner’s needs.
Boh Bros. Construction has worked several design-build projects in the highway/heavy market, but it has rarely been responsible for design in an industrial setting. “Industrial design-build projects are inherently more complicated than typical highway/heavy projects, so it takes the right arrangement to stay on track,” says Jeff Plauche, Boh’s senior vice president of preconstruction. “This project needed the right team—owner, designer, and contractor all playing their parts, working as one, to be successful. We certainly achieved that here,” Plauche says.
The design build arrangement enabled the project team to swiftly clear a variety of hurdles, including supply chain disruptions, the threat of four hurricanes and the COVID-19 pandemic—without missing a single day. “Being so closely integrated with Vopak Moda and our design partner, Lanier & Associates, enabled us to quickly respond and resolve any challenge. Even during the early days of the Covid-19 pandemic, we were able to establish new site protocols and communication procedures amongst the team to press on without delay,” Plauche adds. “Nobody left and nobody went home. The schedule was uninterrupted.”
A secondary benefit of the pandemic was the necessity for the team to lean more heavily on Microsoft Teams, Zoom and other collaborative tools. They were already using Procore and other systems, but COVID-19 forced them to elevate their usage to a new level. It became a tremendous advantage for the remote project, as the team could routinely pull up live views of the site, display testing reports etc., all in real time.
Now complete, the new VMH facility consists of a 250-foot-long, all-precast approach way, 85- by 60-foot ship dock and 56- by 36-foot barge dock, and supports the owner’s new deep water crude oil and refined products storage terminal. The facility will handle various hydrocarbons, refined products, and petrochemical feedstocks, and is strategically positioned near the largest refining and petrochemical complex in the U.S.
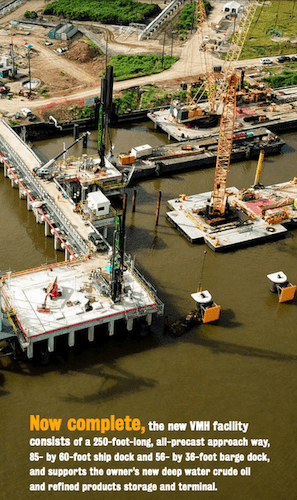
Clearing Hurdles
To win the project, Boh’s piling and marine group value engineered some $1 million off the job cost during the bid phase, then began an aggressive design process with the assistance of Lanier & Associates Consulting Engineers to get plans to 100 percent. After receiving approval from Vopak Moda in early 2020, the project was able to proceed.
That’s when the challenges began. Grant Closson, Boh project manager, had just begun procuring materials in spring 2020 when COVID-19 put the nation under lockdown. And while some of the long-lead items—sheet piles for the bulkhead, in particular—were already designed and procured, most everything else was up in the air. “Nobody knew who was going to be closed down or for how long,” Closson says, “so we cast a big net, reaching out to suppliers wherever we could find them.
“There were a lot of unknowns. The rebar supplier couldn’t find truck drivers and the guys supplying the imbedded steel items had to shut their plant down…and that slowed down the pile deliveries. It all snowballed.” Boh re-sequenced the schedule when possible to accommodate longer-than-expected delivery dates. “We ended up constructing the barge dock before the ship dock because it required smaller piles that were easier to find,” Closson says. “We also had to wait on the steel piles to be fabricated for the dolphins.”
Then there were the hurricanes. As many as four storms threatened the site in 2020, each time causing three to four days of delays. Boh treated each storm as if it could be a direct hit—securing barges, storing loose items, etc. “Most of them were pretty big scares, because the forecast models were all over the place,” says Tri Le, Boh’s project manager at the site. “We couldn’t tell if they were coming to New Orleans or Texas; we just didn’t know. Also, 90 percent of our crew was from New Orleans, so trying to stay productive while letting them all go home was part of the process.”
Through it all, the start date and the targeted finish date remained unchanged. “In fact, we would’ve finished a month or two early, but delivery hiccups and hurricanes changed all that,” Closson says.
Working from Water
Boh didn’t have room on the small site for a land-based crane nor could they bring in much material by truck due to a tight turning radius. Therefore, most of the construction was performed from the water, with three barges at the site at any given time—a main crane barge and two separate material barges.
After a land-side clearing and grubbing phase, the Boh team drove 70-foot-long, 1-inch-thick sheet piles for an 875-foot-long bulkhead, then began building the all-precast dock approach way in complete sections, end to end, including piles, caps and deck panels.
Waskey Bridges Inc. of Baton Rouge fabricated and delivered most of the precast pieces to the site, while Flexicore of Texas supplied the piles. Scheduling was critical, as the project team had to be ready for the materials as they arrived. Quality control was equally paramount— “We had to keep everything plumb and the piles in tolerance in order for the precast pieces to fit inside the caps,” Le says. “That was tricky.”
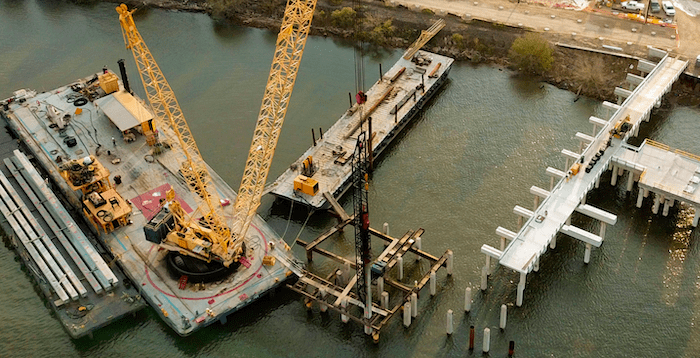
Due to the lack of space, Boh used the services of a stevedoring company across the Houston Ship Channel to load most of the concrete piles onto barges for delivery. To accommodate ship arrivals, the Boh team would frequently accelerate or decelerate its schedule to make it work. “We would adjust our work schedule, increase production, slow it down etc.… whatever we had to do to hit that mark,” Le said.
They also had to coordinate closely with a channel dredging company (working under a separate contract with VMH) to ensure the project’s critical path was never impacted.
“We meticulously planned ahead to keep things going,” Le says. “Being this far from our yard in New Orleans amplified the need to keep material onsite, ready to be installed.”
Once at the site, the maneuvering, lifting, and placing of the super-long concrete piles created challenges of their own. Some of the piles for the ship dock were 30-inch square and 134 feet long, so lifting and standing them vertically was a delicate operation. “We had a crane with 240 foot of boom and 134-foot-long piles,” Le says. “That’s a process right there…just to stand them up and not damage them.”
Another issue—contending with the gradual sloping of the bottom of the Houston Ship Channel. “The piles tried to walk down the slope as we were driving them,” Le says. “We had a pile template, but the piles were big and long. If they started sliding down the slope there was no recovering them.”
Through it all, there was always the potential that they’d damage a pile, so Boh leaned heavily upon one of its pile driving crewmen to coordinate surveying and quality control during the operation. In that role, he would double and triple check the templates to ensure they didn’t move from one day to the next.
Steel breasting and mooring piles comprised the rest of the subsurface work, including eight 84-inch-diameter steel piles by 140 feet long, four for the fender and four for the mooring. All the large-diameter piles were supplied by a fabricator about 5 or 6 miles down the Houston Ship Channel. For all the pile driving, Boh used one of its 300-ton, barge-mounted ringer crane, along with the largest diesel hammer in its inventory—a D 138.
The docks, themselves, were mostly constructed of poured in place concrete—although precast deck panels were used to act as the bottom formwork, requiring the crews to form around the outer perimeter only. The concrete for the deck itself was transported via a pump truck and placement boom from a long distance at high pressure.
In additional work, Boh installed a firewater platform, ship dock gangway platform, and a barge dock gangway platform.
The VMH dock project was completed in June, Plauche says, due to a successfully executed design-build process. “This was a challenging way to build a project, but we had the right team for the job,” he adds. “It wouldn’t have been possible without the seamless relationship between our project management team, Vopak Moda, Lanier, and other contractors on site. Everybody had to work for the interest of the project, not their own. This is a great example of how to do design-build correctly, and certainly a hallmark project for us.”
The success of the effort at the Houston Ship Channel is already reaping benefits. Boh Bros. recently landed another project in Ingleside, Texas with an affiliate of one of the VMH owners.
This article was origionally published in the Summer 2021 The Boh Picture. You can read more about Boh Bro’s projects here.