Swamp Maneuvers
Boh Performs Utility and Paving Work as New Terminal Nears Spring 2019 Opening
For two years now, the joint venture partnership of Hunt Gibbs Boh Metro has sidestepped obstacles of logistics, scope, and cost in constructing the new $1 billion North Terminal at Louis Armstrong New Orleans International Airport.
The project is a hybrid, of sorts, that marries the disciplines of utility, building, apron paving, and road construction.
Despite the hurdles, success is in sight. The JV team is eyeing an early 2019 completion date for the 972,000-square-foot facility. Once operational, the new terminal will include 35 gates, a 2,190-car parking garage, central utility plant, and ground transportation staging area. Portions of the existing facility, including the parking garages, will eventually be repurposed to support the new complex.
The project has become a showcase for Construction Management at Risk (CMAR), as it is the largest such project to be awarded in the state. CMAR is an integrated team approach to planning, design, and construction of a project, and serves the dual purpose of controlling schedule and budget, as well as ensuring quality for the owner.
Lead joint venture partner AECOM Hunt Construction Group has extensive experience working on CMAR projects—79 percent of its most recent annual revenue was earned under CMAR contracts. Boh Bros. is no stranger to CMAR either and is self-performing the entirety of the potable and firewater supply, stormwater and sanitary sewers, and concrete and asphalt paving, for both the landside and airside portions of the project. Still, the terminal project came with a few challenges.
“The first guaranteed maximum price (GMP) was over budget by about $100 million, so it was not an awardable job,” says Boh’s Jeff Quebedeaux, vice president of utilities and paving. “The mayor called in the team and said, ‘Make it happen.’”
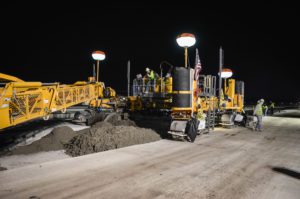
During the next four months of intensive value engineering (VE), CMAR’s resiliency was put to the test. Ideas were vetted, then accepted or thrown out, and changes were made to wrangle the budget into something manageable. For Boh, that meant offering its experience with alternate specifications for drainage components and pavement sections.
“The VE process seemed like eight months wrapped into four,” Quebedeaux says. “We’d have a meeting one day and offer priced alternatives by close of business the next day. For example, we suggested an alternate catch basin design that saved a couple million dollars. It all adds up because of the volume of work.”
There were also significant additions to scope. A new concourse was added about six months into the project, resulting in additional utilities and another 40,000 square yards of accompanying pavement.
AECOM Hunt Construction Group’s Chris Bauer, project executive for the JV team, says one of the more significant challenges has been coordinating the 150-plus contractors working across the diverse, 26-acre job site. Contractors maneuver through the site daily to perform dramatically different tasks. For Boh, that means paving and installing utilities in close proximity to building trades in the nearby terminal.
The coordination took numerous meetings and an unprecedented level of collaboration to make it work. Tim Lewellen, Boh’s paving project manager adds, “Boh supervisors met at 6:30 every morning to plan for safety, quality, and production. We would take this information to a meeting of all JV subcontractors to coordinate critical path activities.” Every team member is represented at the meeting.
Along the way, Boh’s experience in CMAR and with complex projects has proven beneficial. “We have three local partners who have helped us work through the challenges of the ‘localisms,’ i.e. permitting, relationships, working in this environment, etc.,” Bauer says. “Boh has done whatever is needed, such as quickly increasing or decreasing manpower, re-working the schedule, etc., and juggling all of the moving parts. I know it has been a challenge, and they’ve certainly been able to work through it.”
Of course, there’s also a very real financial reason for making it happen—there’s a $96,000 per-day penalty for not completing the project on time.
Building in a Swamp
The expansive site’s unstable soil was a primary concern from the beginning, despite the early placement of a sand surcharge. “Building in a swamp lends itself to a variety of challenges,” Bauer says. “We had a whole year of importing sand and driving piles, but the conditions were still different than expected.” Underground obstructions were also common, such as the discovery of several cypress tree stumps—some larger than a bulldozer.
Through it all, ground settling was an ongoing challenge. When Boh began installing a large box culvert through the middle of the airfield in Summer 2016, the culvert began to settle rapidly. Quickly devising a solution, the team beefed up the foundation to include oak mats topped with 2.5 feet of rock wrapped in fabric. The concrete paving operation was not immune to settling, either. “In the end, it was decided to pave it quickly and let it settle uniformly,” Lewellen says. “Everything went down together, so there wasn’t a bunch of cracks in the pavement.”
Carey Capdeville, Boh’s paving superintendent, says the task of sequencing and coordinating the paving operation was daunting, despite the placements occurring mostly at night. This is not Capdeville’s first experience working at the airport, as he completed a runway there just prior to Hurricane Katrina in 2005. “You have to worry about getting your trucks to you every night,” he adds. “We had to make sure areas were clear and all access roads were clear.” About 12 to 14 dump trucks were used to transport the concrete to the paver.
A new G&Z paving machine purchased specifically for the project performed admirably. “We had a Cadillac for a paver,” Capdeville says. “It’ll go into a counter-rotate mode and spin 360 degrees inside its own tracks. That allowed us to get off of a lane, make a quick U-turn and start paving again within five minutes. The quickest turnaround was 3.8 minutes.”
Paving widths at the airport site measured 18 feet, 9 inches, even though the machine is capable of paving as wide as 30 feet. By the time it was over, a total of 180,000 cubic yards of concrete had been placed for the paved areas, all to FAA specifications.
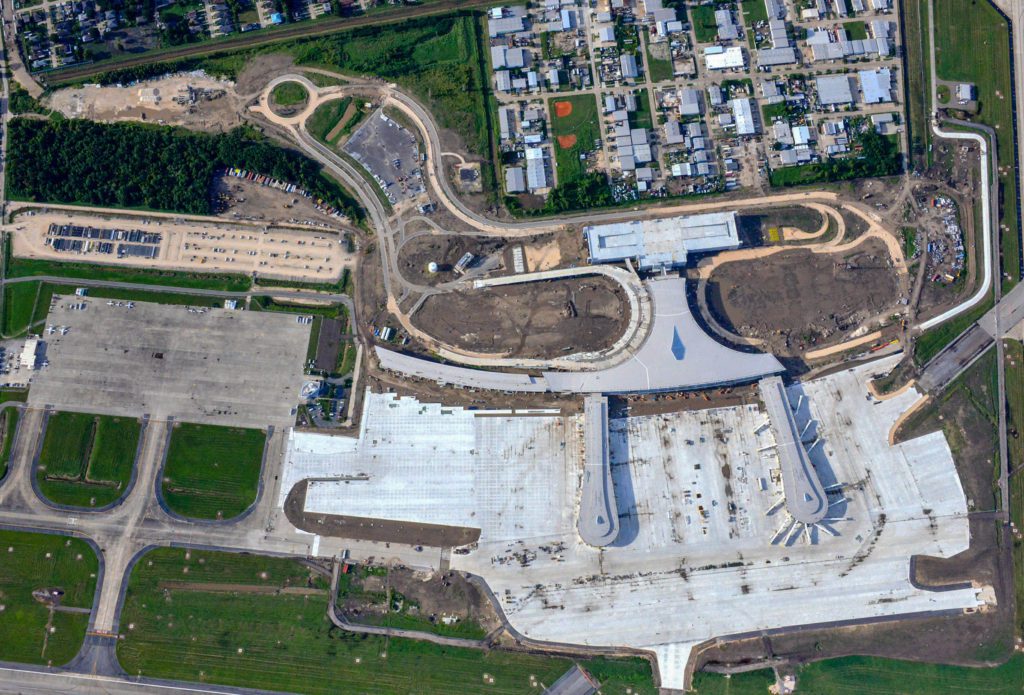
Throughout the process, Boh was careful to monitor for Foreign Object Debris (FOD), a potentially hazardous problem for aircraft that will one day use the apron. Test sections of pavement were cored every 15 feet to ensure that the aggregate was evenly distributed below the surface.
The bulk of the paving was performed over a three month period beginning in late January 2018, all at night in 10-hour increments. “We paved four days a week and took one day a week for maintenance,” Lewellen says. “That eliminated a lot of potential interruptions, and the quality and production were better.” The Boh team mixed cement into the sand to create a work platform, a process never before attempted in Louisiana. In the process, the team re-used sand from the surcharge to save on cost.
Now complete, the pavement system consists of 4 feet of sand, 1 foot of soil cement, 7 inches of lean concrete and 17 inches of surface concrete, all produced by three on-site batch plants.
Accessing the New Terminal
For vehicular traffic, Boh is constructing asphalt feeder roads and a massive roundabout to channel traffic flow to the airport from Loyola Drive. Until a new flyover ramp from I-10 at Loyola Drive is completed, drivers will access the new terminal via I-10 at the Loyola Drive exit in Kenner.
The Louisiana Department of Transportation and Development has been working to extend Loyola Drive to connect to the airport as well as widening its lanes to accommodate more traffic. In January, Gov. John Bel Edwards announced that the new flyover was one of four projects included in a $600 million bond request.
Upon arriving at the terminal, visitors will be greeted by a world-class facility designed by Pelli Clarke Pelli Architects, Manning Architects and the Crescent City Aviation Team, a joint venture of Leo A. Daly Company and Atkins North America Inc. The terminal, with its towering ceilings and open floor plan, will feature a glass facade with wide views of the airfield. Natural light, allowed in by the impressive skylight, will illuminate the main arrivals hall. Unique to the design of the airport, food and retail will be located down the center of each concourse instead of pushed to the side. This will allow for increased visibility of gates, tastes of New Orleans, and shopping.
The terminal will also feature a single, consolidated security checkpoint, which all passengers will enter regardless of their destination or airline. This consolidated checkpoint will increase the efficiency and ease of passengers going through security. Once through the security checkpoint, passengers will be able to move freely among the airports three concourses, giving them the ability to enjoy all the tastes, sights, and sounds that represent our city.
This article was originally published in The Boh Picture. To read about more of Boh’s projects, click here.