CMAR Solution: Project Team Tackles The Causeway Shoulders with Collaboration, Creativity
CMAR Solution: Project Team Tackles The Causeway Shoulders with Collaboration, Creativity
For any project on the heavily traveled Lake Pontchartrain Causeway, there are two equally formidable challenges—weather and traffic. And when the longest bridge in the U.S. needed its most significant upgrade in half a century, the Causeway Commission turned to Construction Management at Risk (CMAR) to get the job done.
The end goal is to build twelve, 1,008-foot-long shoulders, six on the northbound bridge and six on the southbound bridge, to provide much-needed relief to stranded motorists. Until now, a series of seven crossovers linking the two spans have provided the only way for travelers to get out of the main lanes of traffic during an emergency.
The shoulders are long overdue. The first bridge was completed in 1956 when the annual traffic count was only about 200,000 cars. Today, it’s 12 million. “The Causeway is at capacity every morning and evening,” says Causeway General Manager Carlton Dufrechou. “There are about 3,500 plus vehicles per lane during rush hour. And every day, we have eight to ten breakdowns.”
The potential for danger is high, as the existing crossovers were never intended to be emergency stopping areas. They don’t have on- or off-ramps and require that traffic come to a near full stop in order to make a 90-degree turn.
For the Causeway Commission, it quickly became obvious that a CMAR approach to the project would best address their concerns, and provide the most collaborative, comprehensive approach to constructing the shoulders. An integrated team approach to planning, design, and construction, CMAR serves the multi-pronged purpose of addressing risk, controlling schedule and budget, and ensuring quality for the owner.
Dufrechou says the use of CMAR expedited the design and planning phases, and allowed the project team to troubleshoot some key challenges much earlier than the traditional design-bid-build approach. “We cannot close this bridge down. Our mission is to get our commuters back and forth safely and timely. That was the driver behind this.
CMAR statutes dictate that the owner hire a design engineer and contractor through independent contracts, who in turn work together to maximize the efficiency of the design. As such, the commission first submitted Requests for Qualifications for the design, then selected Volkert Inc. of Mobile, Ala., from a short list of qualified applicants. In April 2018, the commission selected Boh Bros. as its pre-construction contractor. Huval & Associates of Lafayette, the project manager for the Commission, and CEC Inc. of Lafayette, the independent cost estimator, round out the team.
G. J. Schexnayder, Group Manager—Heavy Construction, says Boh’s Statement of Qualifications was graded and scored to narrow the list down to three contractors. The SOQ decision was “100 percent qualifications based,” according to a contractor’s key personnel resumes, past project experience and understanding of the project. Following an interview, the Causeway Commission awarded the $200,000 preconstruction services contract to Boh.
In the months that followed, Boh collaborated with Volkert and the Commission on constructability, schedule and budget to help guide the design. Throughout the CMAR process, intensive owner involvement was crucial.
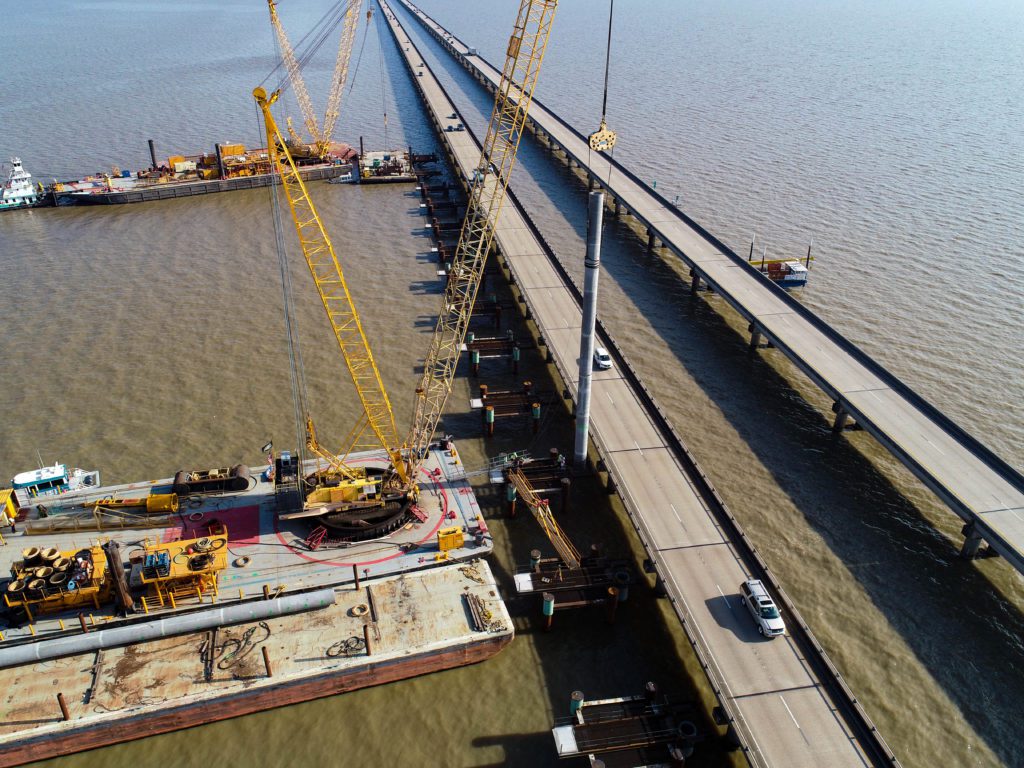
The Causeway team held weekly meetings with all the stakeholders, with the owner present and participating in most decisions. As a result, there wasn’t a lot of waiting, thinking and analyzing. “We would call in the expertise we needed depending upon the topic of the meeting,” Schexnayder says. “If we were talking about pile driving we would bring in a lot of pile driving guys, for example. Or if it was related to the super structure, we would bring in the guys that did the super structure work.”
Through it all, transparency is paramount when addressing and resolving risk. One concern on any project is pile length variability and whether the piles can be driven to grade. “In a low bid world, the contractor assumes the risk of pile cutoff, should the pile meet refusal before reaching designed tip elevation. In that case, if a contractor thinks they’re going to have 100 piles hit refusal and need to be cut (in a low bid environment), they’re going to put the cost of cutting those 100 piles in their job, and the owner is going to pay that whether they cut 25, 75 or even 150 piles.
“But if we break that out as a risk item in CMAR, and don’t include the pile cutoff cost in our bid, then we’ll get reimbursed for only those pile cutoffs that occur. If we cut 25 piles, the owner pays for 25, not 100.”
A police presence at the site, a requirement on any Causeway job, was another risk item addressed by CMAR. Causeway specifications requires one to three police officers on the bridge, solely dedicated to the project. “They elected to take that as a risk item as well, so they only pay for it when we use it.” Schexnayder points out that the risk items aren’t just a blank check, as all are coordinated and cleared daily with the owner’s representative.
A Minimally Invasive Approach
Boh was a crucial part of the pre-construction process, as the contractor’s engineering background enabled the team to make changes more easily. “We have a built-in appreciation for how changes impact design,” Schexnayder says. “That better enables us to suggest solutions that work for both the contractor and designer.”
The CMAR process also allowed for a more expedited design and planning phase and facilitated a construction schedule that minimally impacted traffic. As a result, the project moved quickly from pre-construction to construction in less than nine months, a process that would have undoubtedly taken longer by other means.
Along the way, the team looked for ways to shorten the schedule through Advance Work Packages, such as casting three 120-foot-long test piles in Summer 2018 to facilitate pile driving immediately after the notice to proceed and purchasing 80 percent of the remaining pile lengths prior to an executed GMP (Guaranteed Maximum Price). “I’d say a good 120 days of time were saved due to early procurement,” says Boh project manager Thad Guidry. All of the spun cast piles are being supplied by Gulf Coast Pre-Stress in Pass Christian, Miss.
In fact, the pre-work packages were structured so that the Causeway Commission had full ownership of purchased materials. “If Boh would have failed to negotiate an agreeable GMP construction contract, the owner would have those pieces already cast and available to use,” Schexnayder says. “They would still recognize the schedule benefit even if it hadn’t worked out with Boh Bros.”
Ultimately, Boh Bros. was awarded the Causeway GMP construction contract, although that was never guaranteed—CMAR guidelines require a commitment by the construction manager to deliver the project for the GMP, regardless of their involvement during preconstruction.
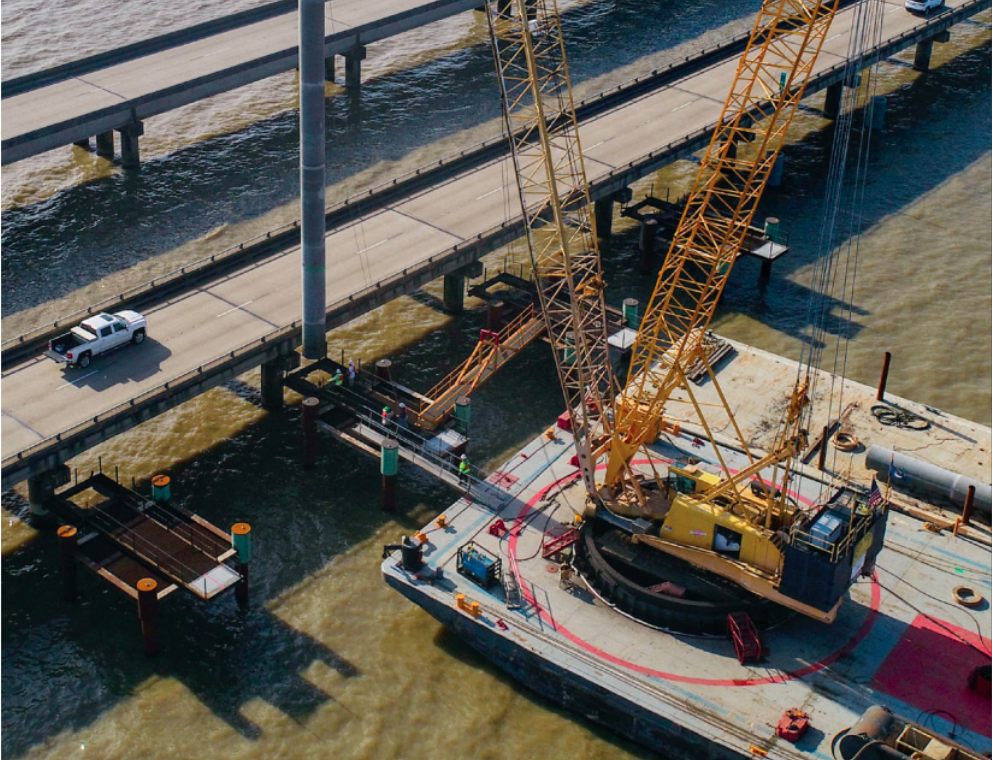
If the preconstruction contractor’s price is significantly higher than the estimate provided by the independent cost estimator, and the owner determines it to be too expensive, the owner can put the project out for bid. In that case, the preconstruction contractor is not allowed to bid on the project.
The team’s most impactful pre-construction decision was to fabricate the bridge sections off-site, in modular fashion, and barge them to the site from Boh’s Almonaster Yard. The ABC (Accelerated Bridge Construction) approach will enable pile driving and pile cap construction to be performed exclusively from the water, thereby circumventing lane closures or shifts. In all, the project scope requires 180 bridge spans (72 in the northbound lanes and 108 in the southbound lanes) from 56 to 84 feet long, supported by 192, 54-inch-diameter cylinder piles ranging from 54 to 112 linear feet.
With the piles and caps in place, the crew will simply float the completed deck pieces to the site. To the average motorist, the shoulders will seemingly materialize overnight. “Tackling one span a night, we’re going to saw cut and remove the existing barrier rail, put the new span in, and in the morning it’s there and it’s safe.” This method allowed the project to meet one of the owner’s main goals, to minimize the impact on daily traffic.
Pile driving at the $45.8 million site kicked off in February, with a notice to proceed in December. Guidry expects pile driving to continue through the summer. “The project is being tackled first in the southbound lanes to stay ahead of a guardrail replacement project being performed by another contractor,” he adds. Project completion is expected by April 2020.
The Causeway Commission’s Dufrechou has been enormously pleased with CMAR. “When I first considered it, I didn’t think it was applicable at all, but I’ve become an advocate,” he says. “It’s certainly working for us. I think we’re going to finish well below the original estimate. It was truly a creative process, and it was interesting to sit in on those sessions and hear the ideas flying back and forth.”
This article was originally published in The Boh Picture. To read about more of Boh’s projects, click here.