Re-Birth: Adaptation of Ship ‘Ways’ Breathes New Life into Avondale
For 75 years, tens of thousands of workers from New Orleans and surrounding parishes commuted to Avondale Shipyards to fabricate everything from fishing boats to large naval vessels. For much of that time, Boh Bros. Construction has had an intimate connection with the facility, completing dozens of projects as part of multiple transformations.
Senior Vice President of Safety Jeff Quebedeaux, a 33-year Boh veteran, has witnessed numerous expansions and revamps over the years. “In the 1990s, we reconfigured the yard so that Avondale could start building double-hulled tankers,” he recalls. “That helped Avondale build the large Panamax vessels that could fit in the Panama Canal.”
There were also greenfield projects—for example, in the early 1990s Boh constructed a 9-acre building that significantly expanded the shipyard’s capacity. In the mid-2000s, Boh performed a large upgrade as part of a $10 million Northrup Grumman project to refurbish the electrical distribution system. Later, the company helped Avondale prepare for the Navy’s LPD warships, one of which was forged from steel taken from the World Trade Center following 9/11.
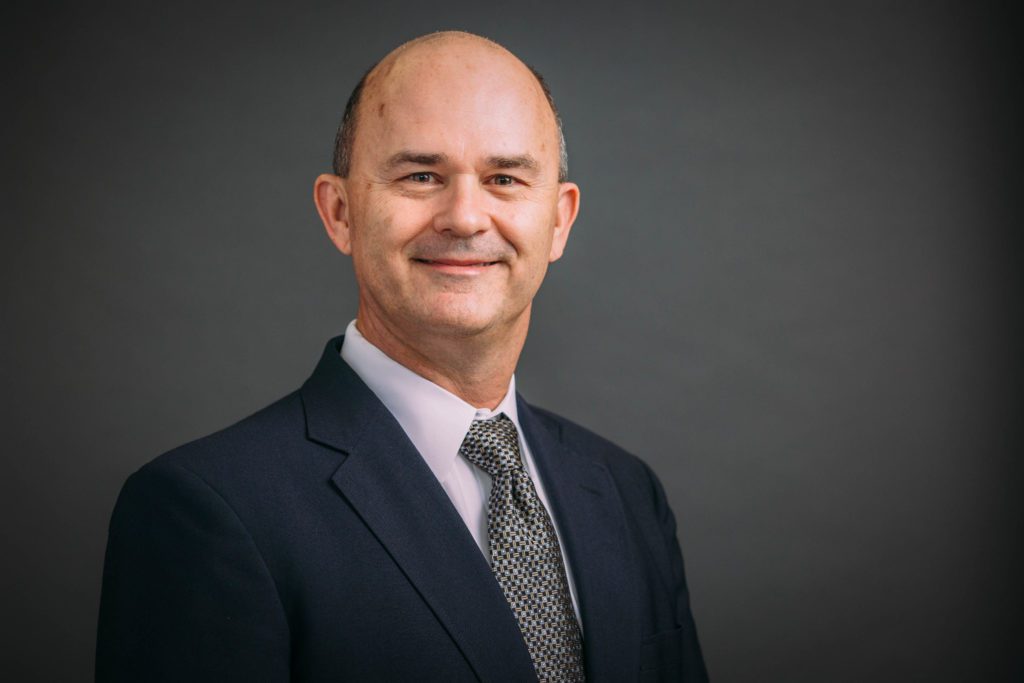
So, when the 254-acre property was shuttered in 2014 it was heartbreaking on many levels. “Avondale was a big part of the West Bank’s economy, and when it shut down it was noticeable,” Quebedeaux says. “You could see its impact everywhere. Shops closed, people moved, and neighborhoods began to decline.”
Fortunately, optimism began to return to the area in 2018, when Avondale Marine—a joint venture of Virginia-based T. Parker Host and Illinois-based Hilco Redevelopment Partners—acquired the property with the promise of revitalizing it into a world-scale logistics hub.
With Boh’s help, Avondale Marine is redeveloping the site’s crane, dock and terminal assets along nearly 8,000 feet of Mississippi River frontage, while connecting global waterborne commerce with manufacturing, fabrication and distribution facilities onshore. In the process, the owners hope to capture connections to six Class I rail carriers in the New Orleans area.
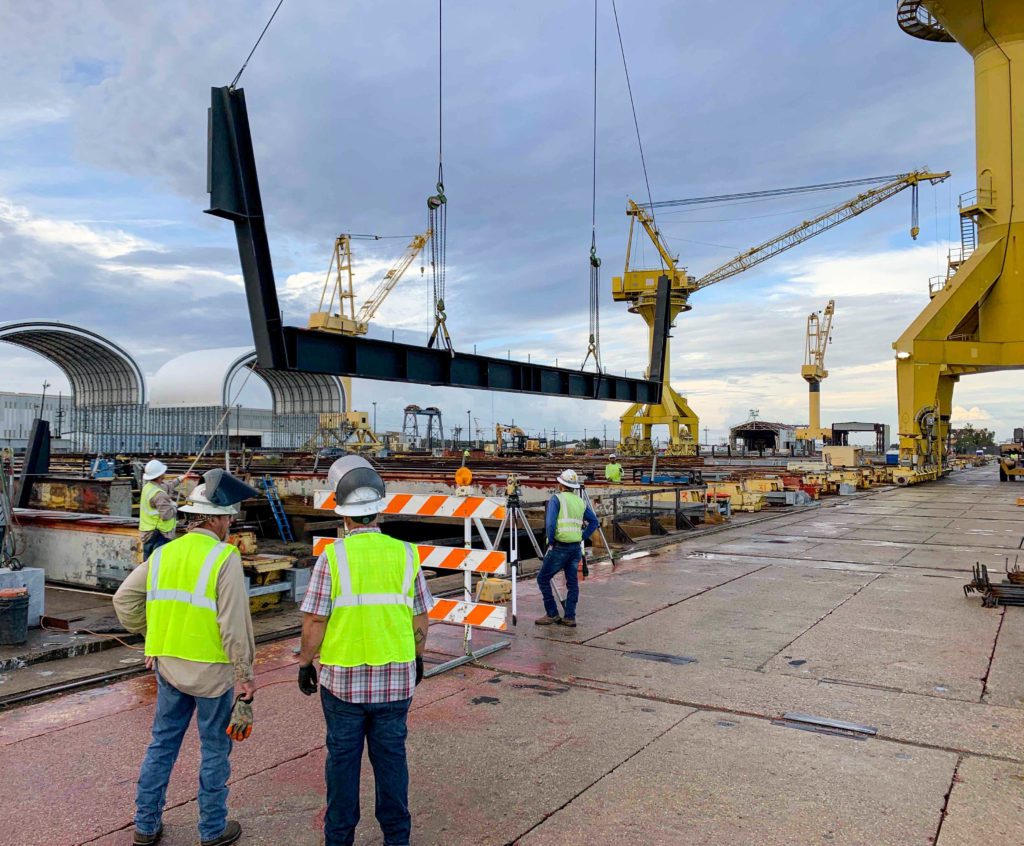
Boh enlisted the use of two existing 300-ton Avondale cranes to assist during demolition, as well as to lift and place the massive precast and steel hangar pieces. By incorporating the cranes, the team avoided the need for barge and land based cranes.
Ultimately, Host plans to turn the site into a multimodal private terminal. In business for nearly a century, the company operates more than 30 maritime agency, terminal, and stevedoring sites, and views the site as a future economic engine for Jefferson Parish and the surrounding region. “Our goal is to place Avondale into the supply chain as a multimodal, global logistics hub that not only moves goods but actually adds value on-site,” says Adam Anderson, president of T. Parker Host, in a press release.
For its part, Boh Bros. is rebuilding Dock No. 2 so that Host can use the dock’s existing pile-supported ship ways to construct a suspended roadway. Once operational, trucks will be able to carry heavy loads from dock to land, and vice versa, as the roadway will have a 100-ton capacity. “We’ll remove the old roadway panels, then install large structural steel hangers and an 18-inch-thick precast roadway,” says Boh project manager Stephen Bernard. “This will allow fully loaded 18-wheelers to access the dock from land.”
In the process, Boh is adapting six of the facility’s 180-foot-long concrete “ways” (large pile caps running perpendicular to the river, previously used for vessel fabrication) to support three suspended roadways. The company plans to construct the roads between each pair of ways and use their bearing capacities as support. Bernard says their foundations are more than adequate, as they were originally designed to handle the weight of a large vessel.
In preparation for the new construction, portions of the ways are demolished and removed to accommodate a widened concrete apron, providing room for the trucks to turn.
In other work, Boh will also install fenders along the dock to support vessels that will moor there while onloading and offloading. This will ultimately prepare the dock for its new purpose. “The idea is to bring a ship to the dock and then bring a truck to the dock. That’s essentially what we’re building for them,” Bernard says.
In the end, the repurposing of the ways will provide Host with greater functionality and enable the owner to achieve a new purpose as a shipping and receiving hub.
Heavy Haul-A Collaborative Approach
New Orleans-based Lanier & Associates Consulting Engineers developed a system to suspend the new roadway off of the existing substructure, resulting in Construction methods were adopted from bridge construction due to the limited space and weight restrictions along the dock. This was more economical design that avoided any conflict with existing infrastructure. Host wanted a versatile roadway that could handle various types of cargo, so Lanier worked collaboratively with Boh to determine the best method for strengthening the roadways from a 25-ton capacity to a 100- ton capacity. The higher capacity will significantly enhance the capabilities of the Host site, once operational. “We came up with this idea of suspending the roadways,” says Robert Massa, a project engineer with Lanier, “but we had no idea what size trucks would ultimately be using them. They gave us some ranges, and we worked from there.”
Lanier teamed with Boh to test various concrete panel thicknesses, and various other structural components, to achieve the desired strength. “We came up with some different ideas to minimize cost and optimize the design by increasing the beam size and increasing the slab size, all with the goal of achieving the capacity requirement,” Bernard says. “We sat down with Lanier to make it all happen…and make it more cost effective.” All totaled, 39 panels were created using a 5,000 psi concrete, along with rather large, No. 11 reinforcing steel. Three panel sizes were needed to achieve the desired configurations.
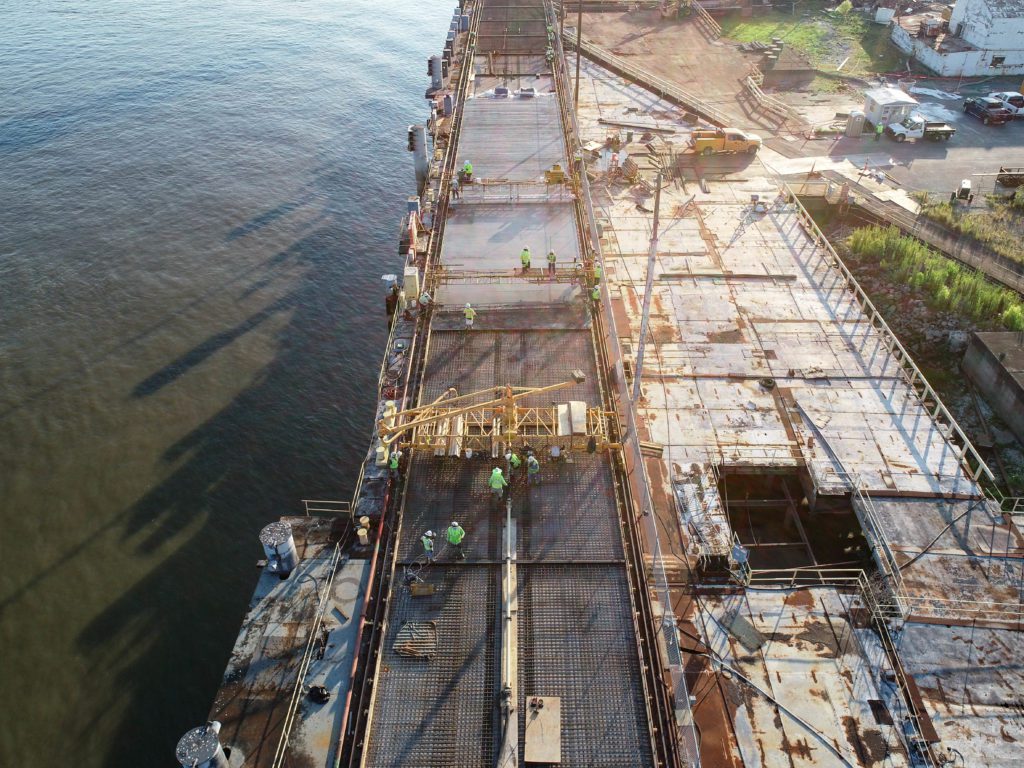
As one of the more cost-significant constructability options, Boh enlisted the use of two existing 300-ton Avondale cranes to assist during demolition, as well as to lift and place the massive precast and steel hangar pieces. By incorporating the cranes—originally used for the vessel fabrication process—the team avoided the need for barge and land-based cranes, thereby saving both time and money.
The Amclyde cranes are atypical to say the least, as they have electric motors, are attached to a long umbilical cord and travel on rails. As such, four Boh operators w participated in a week-long, on-site training session to prepare for the project. “Crane experts were brought in to provide the training, along with some of the crane operators from the old Avondale shipyards,” Bernard says.
Challenges of Logistics and Water
Bernard says work at the site kicked off in December, albeit slowly due to high Mississippi River levels. With the river preventing some phases from moving forward, Boh has instead focused on pre-fabricating the roadways’ massive steel hangers and precast concrete deck panels. Measuring two feet tall and weighing an incredible 176 pounds per foot, the hangars were fabricated in the Almonaster Yard and delivered to the site on trucks. They also fabricated steel beams as diagonal supports for the precast.
While the steel hangars were fabricated at Boh’s Almonaster yard, construction of the precast concrete panels was performed on site utilizing the abundance of available space at the shipyard. The panels were then stored nearby until ready for placement.
When roadway construction begins, the process will move sequentially from landside to dockside. Once the hangers are in place, the installation of the precast roadway panels will follow. Pre-fabricated holes in the panels will enable them to be placed over large Nelson studs and then grouted to prevent any lateral roadway movement. “While the initial plan involved a lot of creativity, the construction itself is fairly typical…precast concrete construction, structural steel fabrication and installation,” Bernard says.
Once operational, the three roadways will be spaced so that the trucks can easily enter by one roadway and exit by another. “The idea is to create a turn around,” Rob Senior Vice President of Heavy Construction says. “A truck comes in, goes to the dock, gets loaded and comes back out by way of one of the other roadways. It’s a big loop.”
In addition to Dock 2 upgrades, Boh also refurbished Wet Docks 3,4, and 5 by installing an 8” thick reinforced concreting topping slab across it. The concrete topping slab increased the dock’s capacity from a 5,000 pound passenger truck to HS-20 loading, which allows for a three-axle semitrailer combination weighing 72,000 pounds. Construction methods were adopted from bridge construction due to the limited space and weight restrictions along the dock. End-on construction techniques were utilized by building each topping section of the dock off of the last completed section. The same concrete placing equipment that was utilized on the Twin Span project was modified to fit this project.
The project was broken up into 9 sections with all four major features of work occurring concurrently along the dock—doweling, resteel, formwork, and concrete placement. Boh also utilized the two existing 120 ton gantry cranes on the dock to provide means for hoisting and moving materials along the dock, which replaced the need for expensive marine cranes and barges. In all, Boh installed 2,200 CY of concrete and 775,000 lbs of resteel in an area measuring 3,020 ft in length and a total of 88,000 sf.
In the face of numerous challenges, the relationship between contractor, engineer and owner made everything possible, says Senior. “If you enter into something like this with a collaborative spirit, you’re going to come out with a better result. Above all else, it’s important to develop a level of trust. Then, you can check every assumption and ultimately get to the best possible goal.” All phases of Boh’s work were finalized in October.
This article was pulled from the Boh Picture. If you’re interested in reading more about Boh Bro’s Projects, click here.