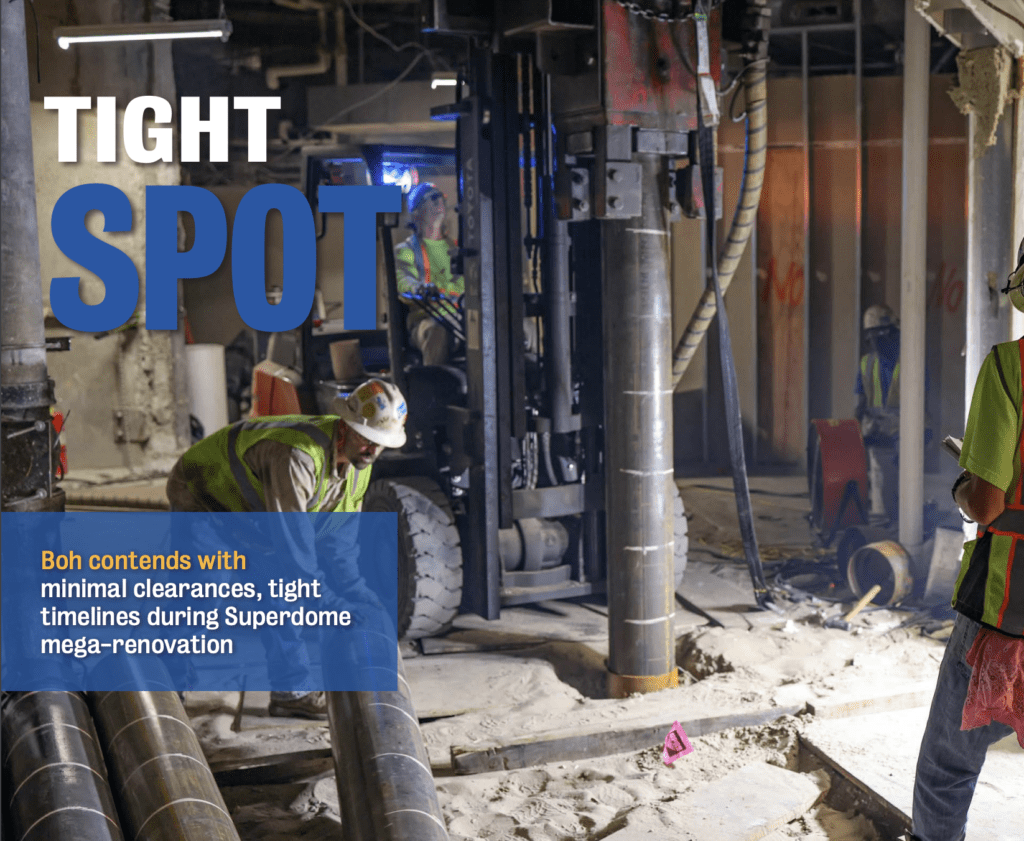
Tight Spot
It’s one of the most high-profile and complex construction projects in New Orleans. Under the guidance of general contractor Broadmoor LLC, the four-year $450 million renovation of Caesars Superdome is a meticulously planned, multiphased endeavor that has continued unabated even during two football seasons and numerous scheduled events.
The deadline is immoveable – the entirety of the renovations must be completed by the 2024 football season – so any challenges must be resolved quickly and efficiently to keep the project moving. Broadmoor’s team of 20 superintendents coordinates daily meetings and weekly pull-planning sessions with the team to keep the project on track.
“During the off season, we go wide open, demolishing, driving piles, and installing and constructing what we can,” says Broadmoor superintendent Charles O’Berry. “Then, during football season we put up temporary walls and work behind the scenes doing finishes, pulling mechanical, electrical, plumbing, etc.”
The extra effort will be worth it in the end. When completed, the interior of the 52-year-old iconic structure will literally be transformed, complete with 16 new elevators, new express escalators and wider concourses that will make it easier for patrons to maneuver through the Superdome’s plaza, loge and terrace levels. There will also be increased food and concession services and new open-air atriums from floor to ceiling in each corner of the stadium. The project will update the facility to modern standards and extend its lifespan for decades.
To provide foundational support for the new elevators, ground-level suites and an electrical substation, Boh Bros. Construction drove some 250, 90-foot-long 3/8-inch steel pipe piles during two of the project’s four phases, most recently this spring and summer. It was often a tricky process, as the Boh team had to deal with minimal overhead clearances, unexpected underground obstructions and no wiggle room in the schedule.
Boh bid each phase competitively with the intention of continuing its success of pile installation at the Superdome dating back to its original date of construction. “Our ability to respond quickly to any situation that arose was particularly beneficial,” says Michael Lagasse, Boh’s piling project manager, having Boh’s main office just a few blocks away. “With a large equipment fleet, we had the ability to replace equipment as needed, the same day.”
The project was sequenced to ensure that the pile driving operation continued uninterrupted. All material deliveries used the same access point, and a designated point person with Broadmoor would coordinate the logistics of the deliveries. “When we were finished an elevator, there would be no down time before moving to the next one,” Lagasse says. “Broadmoor made sure that the foundation was prepped and demolition was complete so we could go from one area to another without any interruption. If our scope was delayed, all work following ours would be delayed.”
When making up for lost time, the Boh team ramped up to 10- to 12-hour days and even worked through Mardi Gras weekend. “The kickoff is a set day,” he adds, “and there was no changing that.”
Broadmoor conducts daily huddles with its subcontractors, which crew numbers, site-wide, averaging about 800. “We cannot fail,” O’Berry says. “In the construction industry, the schedule typically slides a little bit week in and week out. We don’t have that luxury.”
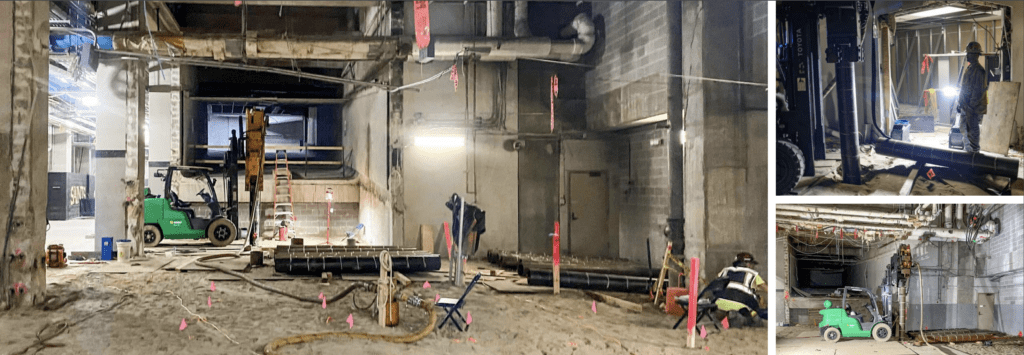
Complex Maneuver
Fabricating, delivering and maneuvering the piles to their various locations within the Superdome was a daunting logistical challenge. Boh measured clearance heights across the site to determine the longest possible length of each section of pile, then fabricated them at the contractor’s Almonaster facility. They then delivered the pieces on 18-wheelers and stockpiled them – in sequence – directly on the Superdome floor.
“The pile pieces were all color coordinated and organized by site based on overhead heights available,” Lagasse says.
Properly prepping the work area was critical to the success of the operation. The Broadmoor demolition subcontractor saw cut each area, then placed and compacted sand in the same space to support Boh’s pile driving equipment. Broadmoor ensured that the contractor had removed all the demolished concrete pieces to facilitate a smooth pile driving process. “It was a clean area when we got there,” says Boh superintendent Brent Pool. “If we had hit a basketball size chunk of concrete, it would have deflected a pile and stopped the operation, costing both time and money.”
The Boh team created a “road” over the sand for its equipment using 4-by-8-foot, 1-inch-thick steel plates. “We had to create a level surface in order to stabilize our equipment,” Pool adds.
Given the tight confines, Boh used two air hammers to drive the piles, supported by small forklifts.
In many cases, and due to extreme limited headroom, numerous splices were needed for a single pile. Near the Team Store at the main entrance, one pile required some 24 splices, with each piece measuring just 3’-6” in length. “There was only 11 feet of working headroom,” Lagasse says. “When the hammer was raised, we were a mere ½ inch from the ceiling.”
Given the volume of work and number of subcontractors working at the site, it took a while to get each pile piece from the field to its driving location which involved multiple people,” Lagasse says. “We had the forklift operator, flaggers etc. and they all had to coordinate with the field superintendent and as many as 15 other subcontractors, all of which were storing equipment and material on the field.
“We would bring in a few pieces of pipe, set them up and stage them in the area … enough for a day or two,” he adds. “The sequence was critical, as it had to be the right pipe and the right size for that site.”
Through it all, third-party inspectors certified the welds and monitored vibrations during pile driving.
To ensure that the project could keep moving, the Boh team always maintained two “roads” of steel plates. When the Boh team hit an obstruction, they’d quickly move to the other row of steel plates and begin driving another pile after alerting Broadmoor of the obstruction. Within minutes, Broadmoor would be at the site, digging a hole by hand to find the obstruction.
“We hit something about 18 feet below grade with the very first pile of the current phase,” Lagasse says. “At that depth, there was no pulling up the pile. We brought in a hydro excavation truck, cleaned the material from the inside of the pile to expose the bottom and identify the obstruction. This allowed for the engineer to make a quick decision on the path forward. In this case, we were able to drive through the obstruction, which was a tree stump, which is common.
By working longer hours and quickly reacting to unexpected challenges, the Boh/Broadmoor team successfully kept the project on track and completed the pile driving on schedule. O’Berry was impressed by Boh’s efficiency and ability to roll with the challenges. “Most contractors will work a solution in a day or two, or longer,” he adds. “But on this job, there has been an attitude of ‘Let’s get it done safely and work collaboratively to keep the job moving forward.’ Synergy is the best way to describe it.”
Recent Comments