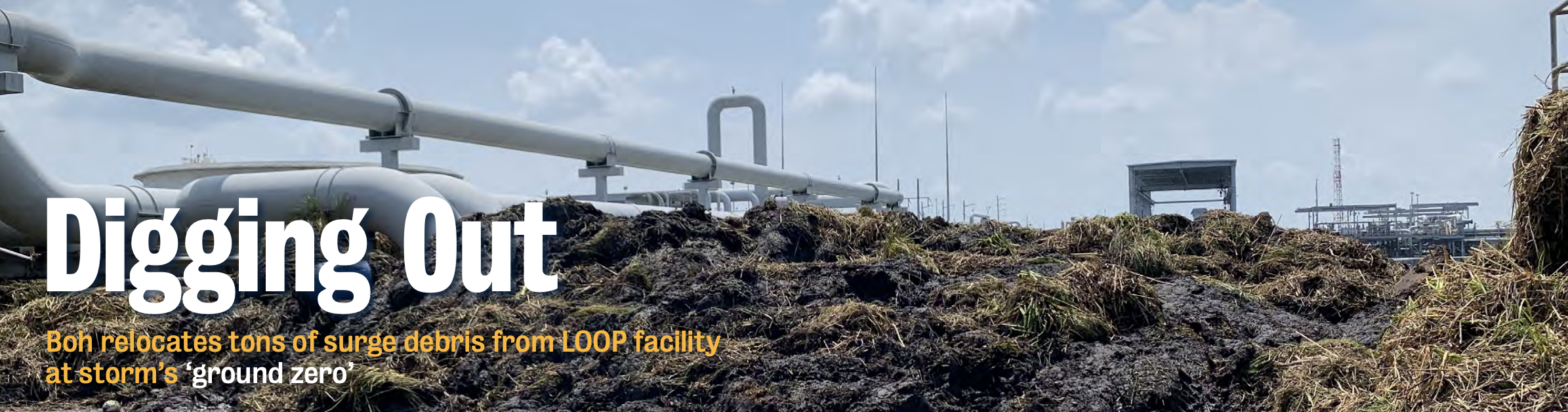
It was nothing but a colossal debris field when the Boh Bros. team first arrived on site to start Surge Debris Removal. Hurricane Ida’s 15-foot storm surge had piled up 4-6′ of odorous marsh mud and grass around the Louisiana Offshore Oil Port (LOOP) facility near Hwy. 308 in Galliano.
All access to the facility had been completely blocked and time was of the essence. The Galliano facility’s pumps, equipment, and pipelines provide a vital onshore link for the LOOP deepwater port some 18 nautical miles off the coast near Port Fourchon. LOOP is an indispensable component of the nation’s energy supply, as it handles 13 percent of the nation’s foreign oil and connects to 50 percent of the U.S. refining capacity.
The owner reached out to Boh about surge debris removal three days after the storm’s Aug. 29 landfall. “They couldn’t access anything,” says Brad Landry, Boh’s project manager at the site. “When the surge came in, it had washed the actual marsh over the entire facility. Their primary goal was to get it back up and running safely with no harm to the environment.”
Construction manager Craig Sanchez, superintendent Dennis LeBlanc and Landry drove to Galliano the next day to get a feel for the project’s scope. They weren’t prepared for what they saw. “When we topped the hurricane protection levee, all we saw was solid marsh,” Landry says. While neither the structure nor equipment had been damaged, much of the facility was submerged in marsh mud and grass.
The team quickly mapped out a plan with LOOP’s guidance, grabbed whatever equipment was available, and cobbled together a team from Boh’s New Orleans and Baton Rouge offices. They got to work just one day later on Sept. 3. “In the beginning, we only had a loader and a mini-excavator down there,” Landry says, “and we focused on the stairways and cleared what we could.” As the scope grew and became clearer, they added excavators, a frontend loader, bulldozer, off-road dump trucks, and a long-reach excavator (for accessing difficult-to-reach areas).
“We weren’t going to move all of that with a shovel,” he adds. “It’s thick mud and marsh grass.”
The Boh team pushed the marshy, mucky material to the side of the access road and began clearing stairways that provide access to the elevated facility platforms, while other contractors worked from the water to clear debris under separate contracts. Boh crews also cleared off a limestone parking lot, while pushing and loading the material into trucks for transport to a staging area.
The surge debris removal went rather quickly and was all executed under the direction of LOOP personnel. An inspector always accompanied the Boh team, flagging existing equipment and piping. For safety, the Boh team added equipment spotters, and in sensitive areas, they used shovels to avoid damaging equipment. “That was critical,” Landry says. “Everything was covered up, and the LOOP guys knew where the equipment was. We were digging and excavating close to their equipment, so we needed to ensure that nothing was damaged.”
The work spanned two weeks of 10-12 hours a day, seven days a week through Labor Day weekend.
A Fluid Situation
Through it all, the nature of the surge debris removal project was continuously evolving. LOOP personnel would meet daily as an Incident Command Staff and established priorities for cleanup, then meet with the Boh team to provide direction. Meetings were always held in the field.
Through it all, Dennis LeBlanc, superintendent, was Boh’s “go-to” guy. “We might be cleaning stairs, roadways, or equipment,” LeBlanc says. “Each day, they’d say the priority was in a particular area, and we’d go to the next thing.”
Since the facility had been shut down during the storm, the condition of much of the equipment was unknown in the beginning. “They needed to get their equipment inspected so they could start everything back up,” he adds. “They would send us all over the place to specific pieces of equipment, such as a pump, electrical panel, etc., that they needed to access.”
One of the primary challenges was the site’s sheer remoteness. The entire area had suffered significant damage, so there was no electricity, fuel, or housing. And cell phone service was spotty at best. “Most areas were down, so communication was tough,” Landry says. “It was hit and miss. We (project management) would lose contact with each other, and we’d have to go somewhere else to get a connection so we could talk.”
Fuel trucks came all the way from Baton Rouge each day to fuel the equipment. Even that wasn’t dependable, as it would often take up to 2.5 hours to get to the site under traffic. “There was a shortage (of fuel) in Baton Rouge as well, so we had to contact some of the local fuel companies to help us out,” Landry says. “We’d fuel up everything when they arrived.”
The team worked from 7 am to 5 pm, then hit the road for home in unpredictable traffic. Much of the traffic was being re-routed due to ongoing utility work at the time. “Traffic was a nightmare,” he adds. “Our entire team had to drive from New Orleans or some other place to get to the site. Many days, they had to drive over two hours to get there.”
Landry was impressed by the dedication of Boh Bros. employees and their ability to come together as a team, at a difficult time, to respond to the needs of the client. “All of these guys had their own personal situations and damage at their homes,” he adds. “They gave up a lot to answer the call from a great client and were mentally and physically tired much of the time.”
But just like after Hurricane Katrina, these guys took pride in serving the community. It didn’t matter if they were from New Orleans or Baton Rouge. They came down here, worked together, and did a phenomenal job.”
Recent Comments