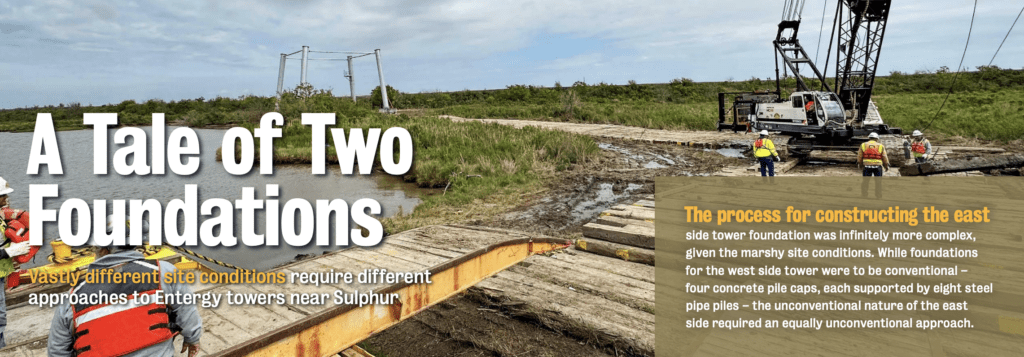
Above ground at least, the two towers carrying a new Entergy transmission line across the Calcasieu River near Sulphur are identical. The similarities end there, though, as vastly different site conditions – solid ground on the west bank and marsh on the east bank – required the Boh Bros. Construction team take decidedly different approaches to constructing their foundations.
It wasn’t the first time for Boh to work on such a project. A year earlier, the contractor had completed foundations for a fast-paced Entergy tower repair job in the New Orleans area in the wake of Hurricane Ida. Earl “Couser” Hano, Boh’s field project manager, says the success of the project was undoubtedly the reason they landed a second capital project with the electrical provider. “Entergy saw firsthand how we worked with everyone, and worked safely, and that definitely played a role,” Hano says. “Another big advantage is we were able to bring some of the same key personnel from the prior job like Todd Topey as concrete superintendent and Anthony Escobar as our site safety representative. Not only were these guys familiar with the work and Entergy, but Entergy was also familiar with them and had trust built in our craft and supervisors.”
It was also helpful that Boh is intimately familiar with Entergy’s site requirements and time constraints, and that
they were one of the few contractors that could mobilize quickly to the scale required.
Contrasting Site Conditions
The process for constructing the east side tower foundation was infinitely more complex, given the marshy
site conditions. While foundations for the west side tower were to be conventional – four concrete pile caps, each supported by eight steel pipe piles – the unconventional nature of the east side required an equally unconventional approach.
Concrete caps were not practical, so engineers planned for the eight-pile configurations beneath each tower leg to be capped by an eight-legged steel grillage weighing some 21,000 pounds. Each grillage would be directly welded to the piles as support for the tower legs.
Turning the design into reality, however, was a daunting challenge overcome only through precise planning and the operation of multiple crews. Once the U.S. Army Corps of Engineers had authorized the work, Boh began ordering crane mats from as far away as Texas and Mississippi, using the west side of the river as a staging area.
At the same time, the contractor’s Almonaster facility in New Orleans began staging equipment to be transported by barge to the site, including 165- and 110-ton crawler cranes, multiple large pile installation hammers, a track hoe, welding machines and leads for the pile driving operation. “Once the barges arrived, our land-based crane on the west bank loaded crane mats onto barges, and our tugboats pushed these barges to the east side,” says Michael Lagasse, Boh’s piling project manager. “We’d push the barge as close as we could to the east side, then our barge-mounted cranes would place the mats in the marsh.”
Steel plates were placed on top of the mats to allow an excavator to continue extending the 30-foot-wide mat road some 500 feet to the tower site. All totaled, some 180 mats were necessary to create the road over a two-day period.
Meanwhile, all the steel pipe piles for both sides of the river were being delivered to the west side. “The west side had a bulkhead, so we could easily throw materials from the land onto the barges and shuttle them across the river,” he adds.
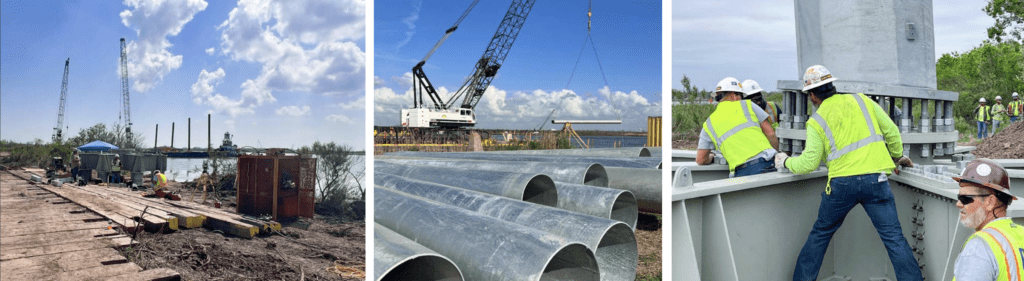
Immoveable Deadline
The Boh team had to move fast, as Entergy had scheduled helicopters to deliver the tower legs on a specific, immoveable date. Therefore, Boh began driving piles on the east and west sides almost simultaneously.
Throughout the process, a tugboat shuttled crews back and forth from the west tower staging area to the barge, and a crane remained on the barge to relay materials, piles, and grillages. “The cranes showed up on a Wednesday, the mat roads were set by that weekend, and by Monday we were driving piles on both sides,” Lagasse says.
“For the east side, we loaded 64 piles onto barges to transport across the river,” he adds. “The piles were then set on the completed mat road and the track hoe moved each piece, as needed, to the installation location for the crane to drive.”
All 24-inch-diameter steel pipe piles had welded splices driven in two pieces for a total length of 80 to 90 feet per pile. The piles for the west side tower piles were driven flush with existing site grades, then encapsulated in concrete, while the east side piles extended above the marsh. The upper 15 feet of each pile was coated with three layers consisting of galvanizing, corrosion protection and UV protection.
Tyler Sykes, Boh’s civil project manager, says the four concrete footings for the west side tower were of a conventional design, each measuring 17 by 17 feet by 4 feet thick. “The trickiest part was making sure the anchor bolts were aligned correctly,” Sykes says. “They’re at a certain angle and must line up perfectly. We used a similar template scheme from the previous Entergy job, fabricated at our Amonaster facility, to set the bolts.”
The grillages for the East side of the river were too wide to be transported by truck, so two of the grillage legs were removed, then re-attached at the site using some 50 heavy-duty bolts for each leg. “The grillage was transported to the west side, loaded onto a barge, then a third crew on the barge prepped each grillage and re-attached the legs.”
Later in the job, Entergy asked the Boh team to drive an additional 30-inch-diameter steel caisson nearly 50 feet away from the east side foundation, which would be a structure for the distribution line feeding tower lighting. “We transported the caisson to the site via barge. It went very well as Entergy quickly requested us to set the four bottom legs,” Lagasse says. “This extra effort reduced the safety risk of using the helicopter to set them.”
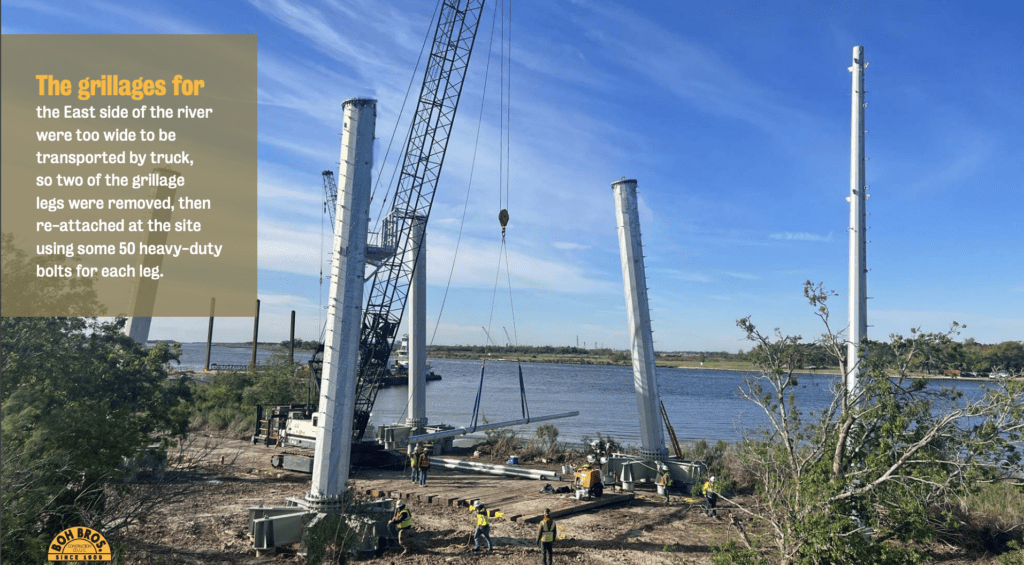
Expecting the Unexpected
The tidal fluctuations and weather were anticipated to be another challenge. Fog or wind would immediately shut down the project. “It was extremely difficult at times … there were one or two days when we couldn’t even get to land due to the low tides,” Hano says. “And if you can’t get close to the shoreline, there’s nothing you can do. We were constantly reviewing the tide ranges.”
Whenever a challenge arose, the Boh Team collaborated closely with EDG, Entergy’s construction manager. Quick decisions were important, as the deadline was set in stone. In the end, everything set perfectly. “We met their schedule, overcame obstacles, and despite the challenges, kept our word by starting and finishing on time,” Lagasse says. It was another successful project with a great team effort.
Recent Comments